The Basic Principles Of Alcast Company
Table of Contents6 Simple Techniques For Alcast CompanyAlcast Company Things To Know Before You Get ThisHow Alcast Company can Save You Time, Stress, and Money.Alcast Company Things To Know Before You Get ThisRumored Buzz on Alcast CompanyLittle Known Questions About Alcast Company.
Chemical Comparison of Cast Aluminum Alloys Silicon promotes castability by decreasing the alloy's melting temperature and enhancing fluidness throughout casting. Furthermore, silicon contributes to the alloy's strength and put on resistance, making it beneficial in applications where resilience is vital, such as vehicle parts and engine components.It also enhances the machinability of the alloy, making it simpler to process right into completed products. In this means, iron adds to the total workability of light weight aluminum alloys. Copper enhances electrical conductivity, making it beneficial in electrical applications. It additionally improves rust resistance and contributes to the alloy's general toughness.
Manganese adds to the strength of light weight aluminum alloys and enhances workability (Aluminum Casting). It is commonly made use of in wrought light weight aluminum products like sheets, extrusions, and accounts. The presence of manganese help in the alloy's formability and resistance to cracking throughout fabrication procedures. Magnesium is a lightweight element that gives stamina and influence resistance to aluminum alloys.
The smart Trick of Alcast Company That Nobody is Talking About
It enables the manufacturing of light-weight parts with superb mechanical buildings. Zinc improves the castability of light weight aluminum alloys and assists regulate the solidification process during spreading. It enhances the alloy's toughness and solidity. It is frequently discovered in applications where complex forms and great information are necessary, such as decorative castings and specific vehicle components.

The key thermal conductivity, tensile toughness, return toughness, and prolongation vary. Amongst the above alloys, A356 has the greatest thermal conductivity, and A380 and ADC12 have the least expensive.
Alcast Company Fundamentals Explained
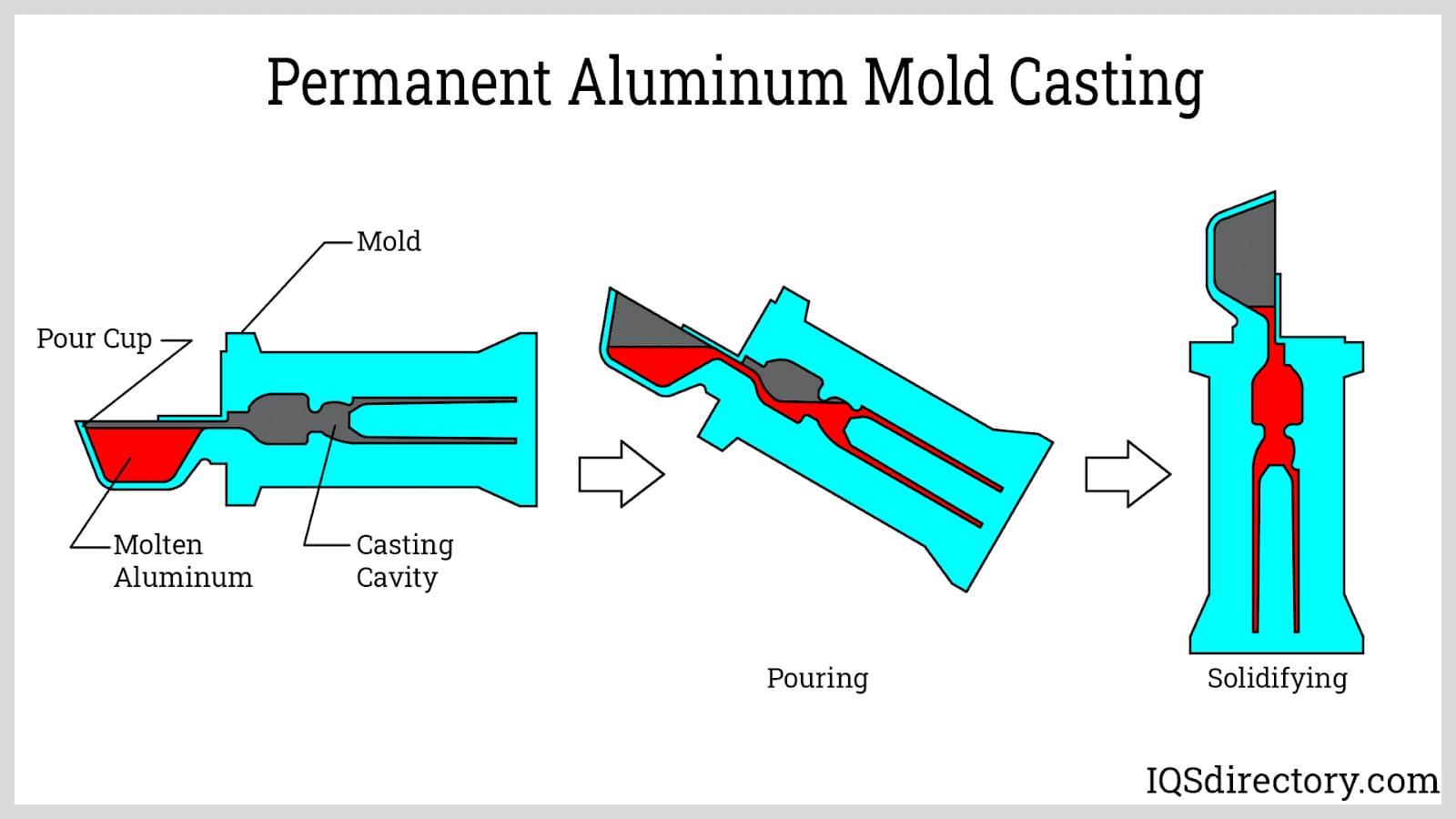
In precision casting, 6063 is appropriate for applications where intricate geometries and high-quality surface coatings are critical. Instances consist of telecommunication enclosures, where the alloy's remarkable formability permits streamlined and aesthetically pleasing layouts while preserving structural honesty. In the Illumination Solutions industry, precision-cast 6063 elements produce sophisticated and effective lights fixtures that need intricate shapes and great thermal efficiency.
It leads to a finer surface coating and better deterioration resistance in A360. The A360 exhibits exceptional elongation, making it optimal for complex and thin-walled elements. In precision casting applications, A360 is appropriate for markets such as Consumer Electronic Devices, Telecommunication, and Power Devices. Its enhanced fluidness enables complex, high-precision elements like smart device housings and interaction tool real estates.
Alcast Company Fundamentals Explained
Its unique properties make A360 an important option for accuracy spreading in these sectors, boosting item resilience and high quality. Casting Foundry. Aluminum alloy 380, or A380, is a widely used casting alloy with a number of distinct features.
In precision casting, aluminum 413 radiates in the Customer Electronics and Power Equipment industries. It's generally utilized to craft complex elements like smart device real estates, electronic camera bodies, and power device cases. Its accuracy is exceptional, with tight tolerances up to 0.01 mm, guaranteeing perfect product assembly. This alloy's exceptional rust resistance makes it a superb option for outdoor applications, making certain durable, long lasting products in the mentioned markets.
The Alcast Company Diaries
The light weight aluminum alloy you choose will significantly influence both the spreading process and the residential properties of the last product. Because of this, you need to make your choice meticulously and take an informed technique.
Establishing the most suitable light weight aluminum alloy for your application will indicate considering a wide range of characteristics. These comparative alloy qualities comply with the North American Die Spreading Association's standards, and we have actually divided them right into 2 groups. The initial group addresses alloy features that influence the production procedure. The 2nd covers attributes influencing the residential properties of the last item.
Some Of Alcast Company
The alloy you select for die casting straight affects numerous aspects of the spreading process, like just how easy the alloy is to function with and if it is prone to casting issues. Hot cracking, likewise referred to as solidification splitting, is a typical die spreading flaw for aluminum alloys that can cause interior or surface-level rips or cracks.
Specific light weight aluminum alloys are much more at risk to hot splitting than others, and your selection ought to consider this. An additional common flaw found in the die casting of light weight aluminum is die soldering, which is when the actors adheres to the die walls and makes ejection tough. It can harm both the cast and the die, so you ought to seek alloys with high anti-soldering buildings.
Corrosion resistance, which is already a noteworthy feature of light weight aluminum, can differ considerably from alloy to alloy and is a vital particular to consider depending on the environmental conditions your product will certainly be exposed to (aluminum casting manufacturer). Use aluminum foundry resistance is one more building generally looked for in light weight aluminum products and can distinguish some alloys